Your team, superior training.
At Riskill we offer a broad range of results-oriented Environmental Health and Safety training; leadership; and team building.
We understand the diverse and unique training needs of your business. Our dynamic, competency-based occupational health, and safety trainings are relevant and engaging.
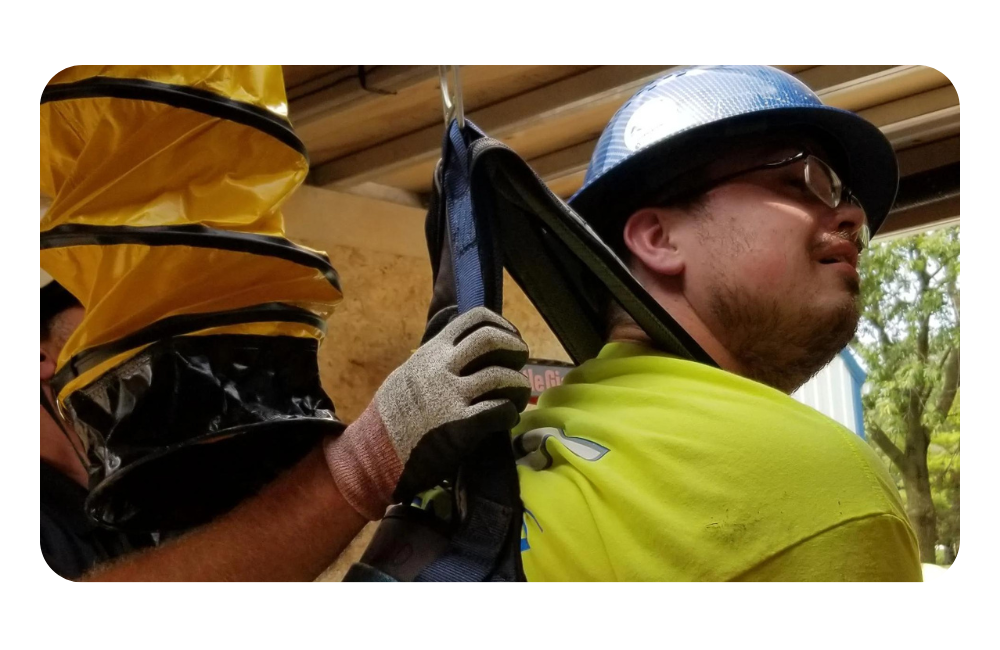
Engaging Course Offerings
We apply the ANSI Z490.1 OSH standard to all of our courses. The ANSI/ASSP Z490.1 standard provides guidance on how to manage overall safety training programs, as well as criteria for developing training that incorporates adult learning principles. Riskill utilizes techniques that include assessing the training program at four levels—reaction, learning, behavior, and results. This is what makes a difference in our approach to training and enables us to ensure we deliver work specific content that the employees can relate to and understand how they will apply it in their work.
Basic Electrical Safety
Course Name | Basic Electrical Safety |
---|---|
Overview | The Basic Electrical Safety course is designed for Non-Electrical Workers.This trainingmodule meets OSHA guidelines fortraining and awareness pertaining topractical safeguarding of employeesin their workplace. This informationis applicable to all electricequipment and installations used toprovide electric power and light foremployee workplaces. |
Duration/Length | 2 Hours |
Target Audience | Employees who work around electrical equipment and installations, but do not directly perform typical electrician or maintenance tasks. |
CFR Reference | 29 CFR 1910: SUBPART “S”, 29 CFR 1926 SUBPART “K” |
Pre-requisites | None |
Course Format | Classroom |
Course Objectives | • The description of basic principles of electricity • Typical electrical hazards and the types of injuries they can cause • Protective measures for avoiding personal injury from electrical hazard • General rules for responding to an electrical emergency |
Electrical Safety for Construction
Overview |
This course teaches electrical safety concepts including the hazard of electric shock and 3 electrical hazard controls. This course explains electrocution and mild electric shock and what they can do to the human body. The three factors determining how severe an electrical hazard is include the amount of current (amps), the current’s path through the body and duration of contact. The goal of this safety course is to reduce or eliminate hazards on construction sites, including temporary wiring, temporary lighting, panels, cords and tools. |
Duration/Length |
2 Hours |
Target Audience |
Workers, foremen, supervisors |
CFR Reference |
29 CFR 1926 Subpart K |
Pre-requisites |
None |
Course Format |
Classroom |
Course Objectives |
Introduction to Electrical Safety What Is Electricity? Electrical Hazards Preventing Electrical Hazards Job Site Hazards Situational Analysis |
NFPA 70E Arc Flash and Electrical Safety for Qualified Employees
Overview |
This is the course for companies needing to formally train employees on the electrical safety requirements contained in OSHA and NFPA 70E standards. This course provides you with an understanding of the requirements outlined by the National Fire Protection Agency (NFPA) 70E for electrical safety in the workplace. You will be able to use this knowledge to improve safety for your employees on NFPA 70E safety standards. This course is designed for supervisors, electrical engineers, electricians, electronic equipment assemblers, industrial machine operators, mechanics, maintenance personnel, safety coordinators and management personnel |
Duration/Length |
8 Hours |
Target Audience |
This course is designed for supervisors, electrical engineers, electricians, electronic equipment assemblers, industrial machine operators, mechanics, maintenance personnel, safety coordinators and management personnel |
CFR Reference |
NFPA 70E, OSHA 1926 Subpart K, OSHA 1910 Subpart S |
Pre-requisites |
None. Electrical experience is beneficial |
Course Format |
Classroom |
Course Objectives |
· Introduction, outline, and provision for practice operation · NFPA 70E introduction and basic concepts · The relationship between NFPA 70E and OSHA · General requirements for electrical safety-related work practices · How to establish an electrically safe work environment · How to work on or near live parts · Safety-related maintenance requirements · Safety requirements for special equipment · The installation of safety requirements · Training requirements · NFPA 70E integration with lockout-tagout procedures · Using the NFPA 70 E Task Lists · Labeling requirements in NFPA 70E and NEC · Energized work permitting |
Lockout Tagout Authorized Employee
Overview |
An effective lockout tagout program goes beyond the locks, tags and devices. In fact, the majority of citations are a result of a lack of proper lockout procedures, training, program documentation, periodic inspections or other procedural elements. This course provides the fundamentals to ensure proper understanding of the essential elements of lockout tagout requirements. |
Duration/Length |
2 Hours |
Target Audience |
Operators, maintenance, supervisors and employees working under lockout tagout. |
CFR Reference |
29 CFR 1910.147 |
Pre-requisites |
None |
Course Format |
Classroom |
Course Objectives |
· Introduction · Definitions · Training · Lockout/Tagout Procedures · Generic Energy Isolation Methods · Restoring Service to Equipment · Locks & Tags · Periodic Inspection · Summary
|
Forklift Operator - Straight Mast
Overview |
The employer is responsible for implementing a training program and ensuring that only trained drivers who have successfully completed the training program are allowed to operate powered industrial forklifts. An evaluation of each trained operator must be conducted during the initial training, at least once every three years and after refresher training. This course is designed to meet the needs of employees and employers by providing the knowledge and skills to operate straight mast forklifts safely. |
Duration/Length |
4 hours |
Target Audience |
Employees who may operate forklifts |
CFR Reference |
29 CFR 1910.178 |
Pre-requisites |
None |
Course Format |
Classroom and hands-on |
Course Objectives |
· Introduction · Proper pre/post operational inspection procedures. · Common forklift accidents. · Awareness of mechanical components and their function. · Safety procedures for picking up loads (load weight, lift capacities). · Load charts · Safety procedures for traveling with loads. · Safety procedures for stacking/placing and dropping loads. · Safety procedures for operating other lift devices. · Discussion on lift truck capacity, load center, center of gravity and steering. · Lift truck classification. Class 4, &5. · Safe loading/unloading procedures. · General safe operating procedures. · How to handle emergency situations · Summary |
Forkift Operator - Rough Terrain
Overview |
The employer is responsible for implementing a training program and ensuring that only trained drivers who have successfully completed the training program are allowed to operate powered industrial forklifts. An evaluation of each trained operator must be conducted during the initial training, at least once every three years and after refresher training. This course is designed to meet the needs of employees and employers by providing the knowledge and skills to operate telescoping boom and straight mast forklifts safely. |
Duration/Length |
5 hours |
Target Audience |
Employees who may operate forklifts |
CFR Reference |
29 CFR 1910.178 |
Pre-requisites |
None |
Course Format |
Classroom and hands-on |
Course Objectives |
Rough Terrain Forklift operation review Main parts and their function Factors affecting stability and capacity Load chart review and exercise Safe operating procedures Pre-use inspections Practical training exercises & evaluations Parking and shut down |
Mobile Elevated Work Platform (Aerial Lift) Operator
Overview |
This is the course for companies needing to formally train operators to use aerial work platforms (scissor and boom lifts). This is the right option if you have new operators and want to ensure they have proper training according to the OSHA standards. If you have existing operators and are unsure of the quality/content of their past training, if you are missing their documentation or if they were certified through a prior employer, this would also be the right option for training. The course includes classroom instruction, written testing and hands-on evaluations for each type of aerial work platform they will be using. We are experts at working around busy schedules and will find a day and time that works for your facility. We show operators why they should work safely and the consequences of what can happen to their health and families if the rules are not followed. The pre-training survey, classroom instruction, hands-on evaluations and all OSHA required follow up paperwork are included in the cost of your training.
|
Duration/Length |
4-5 Hours (Depending on the number of participants) |
Target Audience |
Operators of MEWPs |
CFR Reference |
29 CFR 1926.450-453 |
Pre-requisites |
None |
Course Format |
Classroom and hands-on |
Course Objectives |
· Introduction, outline, and provision for practice operation · Benefits of training · Training vs. familiarization · Management’s role in safety and the operator’s role · Knowing your aerial lift & the importance of reading the operator’s manual · The “big four” safety issues including tip-over, fall, collision and electrocution · Basic components and typical control layouts · Vehicle capacities · The use of fall protection, as it applies to aerial lifts · Operation of emergency ground controls · Ground conditions · Weather related dangers · Pedestrian safety · Operating in tight areas · Basic operational issues · Traveling rules · How to avoid damage to the equipment and facilities · Proper parking · Operation on ramps · Fueling procedures · Personal protective equipment · Pre-shift vehicle and job site inspections
|
Mobile Elevated Work Platform (Aerial Lift) Operator
Overview |
The American National Standards Institute (ANSI) has published new rules governing the design, use, and training of users this year. ANSI published a new standard -ANSI A92.24: Training Requirements for Operators of MEWPs - designed to consolidate all the training requirements from various types of equipment into one standard. These new requirements will become effective in December of this year. The new standards place greater responsibility on the equipment user/owner regardless of whether they are a large maintenance operation or a small business that rents a scissor lift, boom lift, etc. for seasonal work.
Training has some new requirements under this standard: First, training is required for each class of MEWP classification. This means that operators must be provided specific instructions to occupants so they can work safely in an MEWP, including how to use fall protection and the location of fall protection anchors and teaching them how their actions can affect stability.
New training is also required of Supervisors. The standard now requires supervisors of MEWP operators shall receive supervisor training. This shall include:
This is the course for companies needing to formally train supervisors of aerial work platform operators (scissor and boom lifts). The course includes classroom instruction and written testing.
|
Duration/Length |
1 Hour |
Target Audience |
Supervisors of MEWP Operators |
CFR Reference |
29 CFR 1926.450-453 |
Pre-requisites |
None |
Course Format |
Classroom |
Course Objectives |
· Introduction, outline, and provision for practice operation · MEWP classifications, features and applications to assist with the proper selection of the correct MEWP for the work to be performed; · The responsibilities of all parties involved with the operation of MEWPs; · The rules, regulations and standards that apply to MEWPs, including the provisions for safe use as defined in ANSI A92.22, training and familiarization, and the work being performed; · Potential hazards associated with the use of MEWs and the means to protect against, eliminate or mitigate identified hazards; · The requirement for operators to read and understand the appropriate operator’s manual prior to using a MEWP and knowledge that the manual must be properly stored in the weather-resistant compartment on the platform when not in use by the operator.
|
Bucket Truck Operator Safety
Overview |
The Bucket Truck Operator course provides new and experienced industry professionals with the knowledge, skills, and materials necessary to safely operate bucket truck operators on the safe use, inspection, and required maintenance of bucket trucks. During training, participants will utilize Bucket Truck vehicles to perform skill testing, job-related simulations, and scenario-driven aerial lift manipulation exercises. |
Duration/Length |
4 hours |
Target Audience |
New and experienced bucket truck operators |
CFR Reference |
29 CFR 1926.450-453 |
Pre-requisites |
Fall Protection |
Course Format |
Classroom and hands-on |
Course Objectives |
|
Rigging Safety Awareness and Signal Person
Overview |
Employees who work around cranes or hoists and whose job requires them to handle material of all shapes, sizes and configuration are provided training and education in the skills needed to properly perform this job function. Students learn the recommended safe rigging practices and procedures used.
Signal persons are used to simply be a separate set of eyes on the ground, helping the operator get the load from Point A to Point B. Now the person in this position is more accountable to help the whole crew and to ensure the load is taken along a path that minimizes risk to others and lowers the risk to the crane. Signal persons must prove they are capable of signaling by written or oral testing and by performance.
|
Duration/Length |
6-8 Hours |
Target Audience |
Construction and General Industry employees who will be working around cranes/hoists and occasionally perform rigging or signal tasks. Supervisors of these tasks will also benefit from this course. |
CFR Reference |
29 CFR 1926 Subparts N and CC |
Pre-requisites |
None. |
Course Format |
Classroom & Hands-on |
Course Objectives |
· Applicable OSHA & ANSI/ASME Regulations and Standards, · Crane hazard awareness, · Principles of Rigging, · Sling types, uses, limitations and inspections · Rigging hardware types, uses, limitations and inspections, · Safe Operating Practices, · Equipment ratings · Communications in Lifting Operations, · Requirements for OSHA Crane Signaling, · ANSI Hand signals, · Voice Signaling, · Accident Causes and Preventions.
|
Confined Space Safety Awareness
Overview |
This course will provide general awareness on confined spaces, describe a permit-required confined space, and describe the job roles and responsibilities involved in confined space entry.
This session will review the requirements for confined space entry programs, permits, training, gas detection, equipment and rescue. Participants will gain an overview of the required elements of a successful confined space entry program. |
Duration/Length |
3 Hours |
Target Audience |
All audiences |
CFR Reference |
1926.1200 and 1910.146 |
Pre-requisites |
None |
Course Format |
Classroom |
Course Objectives |
• Understand the duties of the attendant, entrant and supervisor • Understand atmospheric hazards and atmospheric testing procedures • Understand the parameters of the electronic gas monitor • Understand the basic properties of the four main gases encountered in a confined space • Understand ventilation techniques • Describe the entry permit
|
Confined Space Entrant/Attendant/Supervisor
Overview |
This confined space entry and operations course is designed to aid the student in better understanding what a confined space is and how to properly identify and work in such spaces. This course studies applicable regulations, typical confined space hazards, control measures and proper equipment selection, inspection and use. This class includes both classroom and practical, hands-on exercises – including basic rescue techniques.
Employees must be trained when first assigned to duties in and around permit spaces; before there is a change in assigned duties; whenever there is a change in operations that presents a hazard; and whenever the permit-space entry procedures change.
Certification of Confined Space Entrant/Attendant training must be available for inspection by employees or their authorized representatives.
|
Duration/Length |
8 Hours |
Target Audience |
Employees who will be participating in confined space entry work, for both non-permit and permit required confined spaces. |
CFR Reference |
29 CFR 1910.146; 29 CFR 1926.1100 |
Pre-requisites |
None |
Course Format |
Classroom Instruction, written test, equipment demonstration, participant entry into the confined space simulator, hands-on participant evaluation. |
Course Objectives |
Upon completion of this training the student will be able to: • Describe the entry permit • Define the system for preparation, issuance, use, and cancellation of the entry permit • Understand permit-required confined spaces • Mitigate hazards encountered while working in a confined space • Instruct workers on the proper use of equipment • Understand the duties of the attendant, entrant and supervisor • Understand atmospheric hazards and atmospheric testing procedures • Understand the parameters of the electronic gas monitor • Understand the basic properties of the four main gases encountered in a confined space • Understand ventilation techniques • Define rescue and emergency procedures |
Confined Space Rescue
Overview |
The Confined Space Rescue Technician course will provide the student with exposure to many common industrial rescue challenges, and new equipment that rescue teams members are not often familiar with. At the Technician level students will be challenged with more complex confined space rescue scenarios. This 5 day course uses a scenario-based interactive approach for training the confined space rescue team members. Trainees are divided into teams at the beginning of the course and work in the same teams throughout the course. On the first day, each team is assigned two confined space scenarios for the Hazard Assessment Workshop. During that workshop, each team performs hazard assessments for their assigned spaces by filling out the first page of a Pre-Emergency Planning Worksheet for each space. The trainees learn about various aspects of confined space rescue as the course progresses. On the final day, the class works in teams to complete the preplanning worksheets, thus completing the process of preplanning the scenario spaces. In the Rescue Rotation Field Exercise each team will be required to utilize information from the preplans to perform a mock rescue from two of the scenario spaces, one horizontal-type space and one vertical-type space.
|
Duration/Length |
5 Days (40 Hours) |
Target Audience |
Emergency Response team members, |
CFR Reference |
OSHA 29 CFR 1910.146; 29 CFR 1926.1100 NFPA 1670 Standard on Operations and Training for Technical Search and Rescue Incidents ANSI Z117 Safety Requirements for Entering Confined Spaces ANSI Z490 Criteria for Accepted Practices in Safety, Health, and Environmental Training |
Pre-requisites |
Fall protection user training. OSHA requires that employees who will function as rescuers have a current first aid/CPR certification. |
Course Format |
Classroom Instruction, written test, equipment demonstration, participant entry into the confined space simulator, hands-on participant evaluation. |
Course Objectives |
At the completion of this training, the student should be capable of hazard recognition, equipment use, and the techniques necessary to operate at confined space rescue incidents. Content includes:
Regulations OSHA 1910.146 and 1910.147, NFPA 350 and 1006 Hazards Rescuer Safety Lockout / Tagout PPE Entry Intermediate Ropes & Rigging: Raising & Lowering Systems, Mechanical Advantage Air monitoring / ventilation Patient Packaging Retrieval methods for non-complex horizontal and vertical spaces Retrieval methods for complex horizontal and vertical spaces Supplied Air Respirators / SCBA Retrieval Systems Incident Command System / Risk Assessment Communications Rescue Scenarios |
Gas Detector User
Overview |
Gas detectors (or gas monitors) are critical pieces of safety equipment used to protect life and property. Using visual and audible alarms, they warn users of atmospheric hazards including dangerous levels of toxic and explosive gases and low oxygen levels. Personal and area gas detectors offer a trustworthy solution for detecting gases that may be invisible and odorless. The training course explains the basics for the use, calibration and daily maintenance of the current portable gas detectors and their accessories. |
Duration/Length |
1 hour |
Target Audience |
Employees who will need to use gas detection occasionally or regularly |
CFR Reference |
29 CFR 1910.146; 29 CFR 1926.1100 |
Pre-requisites |
None |
Course Format |
Classroom & Hands-on |
Course Objectives |
· Fundamentals of gas detection · Sensor principles, calibration and adjustment · Intended use of gas detectors · Expectations · Operation · Button Overview · switch on/off · Operational Screens · user menus · Location services · Identify alarms, notices and errors · Charging battery · Docking station use · Pumped unit & Extended Probe use
|
Hydrogen Sulfide Safety
Overview |
The goal of the Hydrogen Sulfide (H2S) course is to learn how to recognize when Hydrogen Sulfide is present in your work area and to describe the precautions necessary to work with Hydrogen Sulfide safely. This program will help to fulfill the training requirements of API Recommended Practice 49, ANSI Z390.1 and other regulatory standards. |
Duration/Length |
4 hours |
Target Audience |
All employees who may be exposed to H2S |
CFR Reference |
ANSI Z390, 29 CFR 1910.1000(b)(2), 1910.134 |
Pre-requisites |
None |
Course Format |
Classroom, hands-on |
Course Objectives |
The definition of Hydrogen Sulfide, along with its toxicity, common names and how it is formed • State that the common industrial sites where H2S can be found include petrochemical, petroleum exploration and production, manufacturing, and agricultural • State the properties and characteristics of H2S • List the concentrations/toxic levels of H2S according to the ACGIH TLV/TWA, OSHA PEL/ TWA, along with exposure levels and toxic gas comparisons • List the common H2S effects on individuals along with entry routes, susceptibility and hyper susceptibility issues • Compare/contrast the detection and monitoring personal, portable and fixed monitors and detectors including chemical versus electronic instrumentation • Hands on exhibit of SCBA use and limitations • Compare/contrast the types of air supplied respirators, including self-contained breathing apparatus, airline respirator with egress bottle and the escape pack • Discuss the special problems created with the use of corrective glasses/contact lenses, facial hair and facial characteristics • List the medical considerations with wearing an air supplied respirator • Demonstrate proper maintenance and inspection of air supplied respirators • Complete a donning and doffing exercise according to regulatory and company-specific time limits • Discuss rescue, first aid techniques, and post-exposure evaluation, including emergency rescue; rescue breathing and CPR; medical follow-up with students stating the importance of maintaining a valid adult CPR and first aid certification |
Hazard Communication
Overview |
The Hazard Communication (HAZCOM) training module meets OSHA guidelines for training and awareness pertaining to the hazard communications standard, this module fulfills basic requirements for employees who may be exposed to hazardous chemicals. The module further fulfills the basic requirements outlined in Occupational Safety and Health guidelines, Code of Federal Regulations 29 CFR 1910.1200. The course specifically trains employees to know that they are exposed to hazardous chemicals, to read SDS sheets, use and read labels. |
Duration/Length |
2 Hours |
Target Audience |
All employees |
CFR Reference |
29 CFR 1910.1200 |
Pre-requisites |
None |
Course Format |
Classroom |
Course Objectives |
Hazard determination • Hazardous chemical list • Safety Data Sheet(s) (SDS) • Definitions associated with hazard communications • Hazardous Material Labeling System
Students will use actual SDS sheets to determine safety information on simulated chemical container prior to handling the product. |
Bloodborne Pathogens
Overview |
Bloodborne diseases continue to pose major health problems. Increasing infection rates for Hepatitis B and Hepatitis C are now making them as serious a concern as HIV, the virus which can often lead to AIDS. So it’s more important than ever for employees to understand the hazards of bloodborne pathogens, the policies and practices that can prevent their transmission, and the OSHA regulations that address them.
This Bloodborne Pathogens training products provide this essential information while assisting commercial and industrial organizations in fulfilling the training requirements contained in the OSHA Bloodborne Pathogens Standard. |
Duration/Length |
½ hour |
Target Audience |
All employees |
CFR Reference |
29 CFR 1910.1030 |
Pre-requisites |
None |
Course Format |
Classroom |
Course Objectives |
Bloodborne Pathogens: HIV and Hepatitis Infection and the Exposure Control Plan Methods of exposure control. Personal protection and vaccination. Housekeeping and "Regulated Waste". Accidental exposure procedures. |
HAZWOPER Awareness
Overview |
The Hazardous Waste Operations and Emergency Response; Awareness Level (HAZWOPER) 4 hour course provides training and education to employees who participate, or are expected to participate, in emergency response operations for releases or threats of releases of hazardous substances without regard to hazard location or their hazard response level. First responders at the awareness level are individuals who are likely to witness or discover a hazardous substance release and who have been trained to initiate an emergency response sequence by notifying the proper authorities of the release. They would take no further action beyond notifying the authorities of the release. |
Duration/Length |
4 Hours |
Target Audience |
Employees who must recognize the signs of an emergency and initiate the appropriate response plans |
CFR Reference |
29 CFR 1910.120 |
Pre-requisites |
None |
Course Format |
Classroom and hands-on |
Course Objectives |
• Names of personnel and alternates responsible for site safety and health • Safety, health, and other hazards present on the site • Use of personal protective equipment • Work practices by which the employee can minimize risks from hazards • Safe use of engineering controls and equipment on the site • Medical surveillance requirements, including recognition of symptoms and signs which might indicate overexposure to hazards The site safety and health plan required under 1910.120(b)(4)(ii), as follows: • Organizational structure • Comprehensive work plan • Site-specific safety and health plan • Safety and health training program • Medical surveillance program • Employer’s standard operating procedures for safety and health • Any necessary interface between general program and site-specific activities • What hazardous substances are and the risks associated with them in an incident • Potential outcomes associated with an emergency created when hazardous substances are present • Recognizing hazardous substances in an emergency • Identifying the hazardous substance, if possible • The role of the first responder awareness individual in the employer’s emergency response plan including site security and control and the U.S. Department of Transportation’s Emergency Response Guidebook • Recognizing the need for additional resources and notifying the communication center |
HAZWOPER Industrial Emergency Response – Operations Level
Overview |
Emergency response refers to a response effort by designated personnel to an occurrence that results in, or is likely to result in, an uncontrolled release of a hazardous substance. First responders at the operations level are personnel who are likely to witness or discover a hazardous substance release and then initiate an emergency response by notifying the proper authorities of the release and then have the ability to operate within the incident command structure to passively contain or control a leak. |
Duration/Length |
16 Hours |
Target Audience |
Students will be responsible for the recognition of HAZMAT incidents and activation of the emergency response plan. |
CFR Reference |
29 CFR 1910.120 |
Pre-requisites |
None |
Course Format |
Classroom and Hans-on |
Course Objectives |
• HAZWOPER regulations • Safety and health plans • Hazardous chemicals • Safety hazards • Air monitoring • Medical surveillance • Site control • Decontamination • Personal protective equipment • Respiratory equipment |
HAZWOPER Industrial Emergency Response – Technician Level
Overview |
This course is designed to train individuals who respond to releases or potential releases of hazardous substances as part of the initial response to the site for the purpose of protecting nearby persons, property, or the environment from the effects of the release. They are trained to assess and respond in an offensive or defensive fashion while trying to stop the release. Their function is to contain the release from a safe distance, keep it from spreading, prevent exposures, and stop the release. The course covers: an understanding of Hazmat laws and regulations, hazard and risk assessment techniques, selection and proper use of personal protective equipment, understanding of basic hazmat terms, how to perform product control procedures, understanding incident command, and implementing decontamination procedures. This course includes Classroom Instruction, written test, equipment demonstration, participant drills, hands-on participant evaluation. |
Duration/Length |
24 Hours |
Target Audience |
Employees who will be participating in facility emergency response teams and who may be exposed to hazardous substances near the PEL. |
CFR Reference |
29 CFR 1910.120 |
Pre-requisites |
None |
Course Format |
Classroom and Hands-on |
Course Objectives |
• Knowledge of basic hazard and risk assessment techniques. • Know how to select and use proper PPE provided to the first responder operations level. • An understanding of basic hazardous materials terms. • Know how to perform basic control, containment, and/or confinement operations within the capabilities of the resources and PPE available with their unit. • Know how to implement basic decontamination procedures. • An understanding of the relevant standard operating procedures and termination procedures. • Know how to implement the employer’s emergency response plan. • Know the classification, identification, and verification of known and unknown materials by using field survey instruments and equipment. • Be able to function within an assigned role in the Incident Command System (ICS). • Know how to select and use proper specialized chemical PPE provided to the hazardous materials technician. • Understand hazard and risk assessment techniques. • Be able to perform advance control, containment, and/or confinement operations within the capabilities of the resources and PPE available with the unit. • Understand and implement decontamination procedures. • Understand termination procedures. • Understand basic chemical and toxicological terminology and behavior. After initial training, 8 hours of refresher training is required annually to maintain HAZWOPER certification. |
Understanding Chemical Hazards
Overview |
Hazardous materials and waste are part of many work situations, and can be found on many types of job sites. OSHA feels that it is so important for employees to know how to recognize these potentially dangerous substances (as well as how to handle and dispose of them properly) they have mandated that anyone working with these substances receive comprehensive training in this area. |
Duration/Length |
1-1/2 Hour |
Target Audience |
All audiences |
CFR Reference |
1910.1200 |
Pre-requisites |
None |
Course Format |
Classroom |
Course Objectives |
|
Spill Control and Accidental Release Measures
Overview |
As part of its HAZWOPER regulations, OSHA created comprehensive training standards to make sure that employees can recognize, handle and dispose of HAZMATs and hazardous waste safely. |
Duration/Length |
1-3 Hours |
Target Audience |
Employees who work with or around hazardous substances that pose a spill risk. |
CFR Reference |
29 CFR 1910.120 |
Pre-requisites |
None |
Course Format |
Classroom |
Course Objectives |
The Hazard Communication Program. The Emergency Response Plan. The five levels of HAZWOPER emergency response training. Personal protective equipment. Site characterization. Spill cleanup. Decontamination procedures. |
Fall Protection Awareness - Construction
Overview |
The Construction Fall Protection Awareness course fulfills basic requirements for those employees who may be exposed to hazards involving falls. The training also fulfills the basic requirements outlined in Occupational Safety and Health guidelines, Code of Federal Regulations 29 CFR 1926.501, 29 CFR 1926.502 and 29 CFR 1926.503. This program shall enable each employee to recognize the hazards of falling. Each employee will be trained to follow procedures created to minimize hazards from falls. |
Duration/Length |
2 Hours |
Target Audience |
Construction employees of all trades |
CFR Reference |
29 CFR 1926.501, 29 CFR 1926.502 and 29 CFR 1926.503 |
Pre-requisites |
None |
Course Format |
Classroom and hands-on |
Course Objectives |
Fall categories • Fall protection systems • Definitions associated with fall protection equipment • Anchor systems • Inspection, sizing and care of PFAS equipment • Use and care of fall protection equipment
Students must be able to make the selection and use of personal fall arrest systems, put on a full body harness, and know the methods of using a full body harness. The student must also be able to demonstrate the use of a full body harness, properly inspect and store the equipment. |
Fall Protection Awareness – General Industry
Overview |
The Fall Protection Awareness course fulfills basic requirements for those employees who may be exposed to hazards involving falls. The training also fulfills the basic requirements outlined in Occupational Safety and Health guidelines, Code of Federal Regulations 29 CFR 1910 Subpart D – Walking and Working Surfaces. This program shall enable each employee to recognize the hazards of falling. Each employee will be trained to follow procedures created to minimize hazards from falls. |
Duration/Length |
2 Hours |
Target Audience |
Employees exposed to potential fall hazards |
CFR Reference |
29 CFR 1910 Subpart D |
Pre-requisites |
None |
Course Format |
Classroom and hands-on |
Course Objectives |
Fall categories • Fall protection systems • Definitions associated with fall protection equipment • Anchor systems • Inspection, sizing and care of PFAS equipment • Use and care of fall protection equipment
Students must be able to make the selection and use of personal fall arrest systems, put on a full body harness, and know the methods of using a full body harness. The student must also be able to demonstrate the use of a full body harness, properly inspect and store the equipment. |
Excavation Safety / Competent Person
Overview |
According to OSHA 29 CFR 1926 Subpart P, every excavation must have a designated Competent Person to manage the safety aspects of the site. To properly carry out Competent Person responsibilities, this individual must have training in, and be knowledgeable of soil analysis, the use of protective systems, and the requirements of the standard. This course covers safe work practices for excavation and trenching work. It is meant to be used as an introductory or refresher course for construction workers involved in digging or working in an excavation. It is based on OSHA Construction regulations and industry best practices. |
Duration/Length |
8 Hours |
Target Audience |
Designed for All Personnel Involved in Excavations Including Foremen, Superintendents, Engineers and Any Personnel Involved in Underground Projects |
CFR Reference |
29 CFR 1926 Subpart P |
Pre-requisites |
None |
Course Format |
Classroom (Interactive) |
Course Objectives |
▪ Introduction to Trench Safety & the OSHA Excavation Standard ▪ Competent Person Responsibilities ▪ Soils Classification ▪ Sloping, Shoring, Shielding Guidelines ▪ Requirements for Protective Systems & Options ▪ Job Planning & Site Specific Engineering ▪ Confined Space Overview |
OSHA 10 Hour - Construction
Overview |
OSHA's 10 and 30-Hour training curricula have always been the gold standard for the safety and regulatory compliance training employees should have to give them the grounding they need in the areas that OSHA feels are most important.
The OSHA 10 Hour Construction Industry Outreach Training Program is intended to provide an entry level construction worker’s general awareness on recognizing and preventing hazards on a construction site. |
Duration/Length |
10 Hours |
Target Audience |
Entry Level Construction Workers |
CFR Reference |
29 CFR 1926 (multiple subparts) |
Pre-requisites |
None |
Course Format |
Classroom & Hands-on |
Course Objectives |
Recognize worker rights under OSHA Understand employer responsibilities under OSHA Identify and protect against major slip and fall hazards, caught-in or -between hazards, struck-by hazards, hand and power tool hazards, material handling hazards and electrocution hazards Select appropriate PPE (Personal Protective Equipment) and lifesaving equipment Identify major health hazards in the construction industry Recognize the role of the workforce and management in improving the current culture |
OSHA 30 Hour - Construction
Overview |
This OSHA training course is beneficial for workers in construction, building development and other related fields. This OSHA training helps educate workers in identifying, predicting, avoiding, preventing and stopping potential hazards in the workplace. |
Duration/Length |
30 Hours |
Target Audience |
Senior level construction workers, supervisors, foremen and safety managers. |
CFR Reference |
29 CFR 1926 (multiple subparts) |
Pre-requisites |
None |
Course Format |
Classroom & Hands-on |
Course Objectives |
|
Hotwork
Overview |
Based on NFPA 51B and 29 CFR 1926 Subpart Q regarding welding, cutting, brazing, and other hot work, this course is intended to help workers recognize the potential hazards of hot work and avoid injuries and property damage by properly planning, preparing for, and performing hot work.
You might have a single portable welding unit to do an occasional spot welding task, or you may have large electric welders to use in daily production. Whenever welding, cutting, or brazing occurs, everyone involved in the operation must take precautions to prevent fires, explosions, or personal injuries from exposure to toxic fumes. Even in routine metal cutting or repair jobs, workers should always follow established safety procedures and resist the temptation to take shortcuts. |
Duration/Length |
1 Hour |
Target Audience |
All employees who perform welding, cutting, brazing or other hot work activities or those who serve as the fire watch. |
CFR Reference |
29 CFR 1926 Subpart Q |
Pre-requisites |
None |
Course Format |
Classroom |
Course Objectives |
• Welding safety program guidelines • Welding hazards • Safe work practices • Requirement for fire watches where certain conditions exist • Welding safety when working in confined spaces • The importance of housekeeping |
Asbestos Awareness
Overview |
This course describes the most common types of asbestos as well as the hazards asbestos may present. It provides an overview of the history of asbestos use, exposure limits, detection, prevention, and regulation. It also covers some of the potential effects of long-term exposure including asbestosis, lung cancer, and mesothelioma. |
Duration/Length |
2 Hours |
Target Audience |
All employees who may work around asbestos containing materials, and who must be trained on avoiding disturbance of these materials. |
CFR Reference |
29CFR 1910.1001 (j)(7); 29CFR 1926.1101 |
Pre-requisites |
None |
Course Format |
Classroom |
Course Objectives |
• The health effects associated with asbestos exposure • The relationship between smoking and exposure to asbestos producing lung cancer • The quantity, location, manner of use, release, and storage of asbestos, and the specific nature of operations which could result in exposure to asbestos • Engineering controls and work practices associated with the employee’s job assignment • Procedures to protect employees from exposure to asbestos, such as work practices, emergency and cleanup procedures, and personal protective equipment to be used • The purpose, proper use, and limitations of respirators and protective clothing, if appropriate • The purpose and a description of the required medical surveillance program • The content of the standard (§1910.1001), including appendices • The names, addresses and phone numbers of public health organizations that provide information, materials, and/or conduct programs concerning smoking cessation • The requirements for posting signs and affixing labels and the meaning of the required legends for such signs and labels |
Workplace Violence
Overview |
It is impossible to ignore the violent incidents occurring in today’s world. Still, your chances of being involved in an active shooter situation are slim; unfortunately, armed intruders and active shooter incidents are occurring with greater frequency every year. Workplace violence ranks as one of the top causes of death each year in the US Department of Labor statistics. For this reason, it is critical that your employees receive training on how to rapidly respond to an armed intruder or active shooter incident in the workplace. This seminar will cover realistic strategies for employees to deal with an armed intruder. Whether your company has implemented Run-Hide-Fight, Lockdown, Evacuation or other crisis action protocols, it is critical that your company comprehends how to place as many ‘roadblocks’ as possible between your employees and the intruder/shooter to increase your chances of surviving an active shooter event. This session will help your team prepare in several ways: First, it will increase the amount of ‘tools’ for employees by exploring tested and proven methods to increase survivability in these incidents. By increasing employee knowledge, you prepare team members to rapidly respond in an incident and decrease panic and in-action. Second, we will explore scenarios specific to your workplace and deal with realistic and practical actions that apply to your specific surroundings. Employees will take away increased day-to-day awareness, response tactics and mental preparation.
|
Duration/Length |
1.5 – 2 hours |
Target Audience |
All workplaces |
CFR Reference |
29 CFR 1910 and 1926 |
Pre-requisites |
None |
Course Format |
Interactive classroom |
Course Objectives |
• Learn how to recognize workplace violence indicators • Learn how to prevent and prepare for the active shooter threat • Learn to take proper action when confronted with an active shooter • How to properly respond to law enforcement
|
Safety Leadership
Overview |
Safety is not something management does to or for employees. Management commitment to safety is necessary, but true safety excellence requires engagement from personnel throughout the organization, especially the hourly employees. Such engagement in safety benefits the employees as well as the organization. In fact, studies recognize that by focusing organizational effort to cultivate a culture of involvement and participation, zero injuries is achievable. However, safety must become a cooperative process where everyone participates to make the workplace safer. Every worker has something meaningful to contribute, and people will contribute if the climate is right. |
Duration/Length |
Varies |
Target Audience |
This course is designed for both new and experienced supervisors and managers and directors. |
CFR Reference |
|
Pre-requisites |
None |
Course Format |
Interactive, small-group activities |
Course Objectives |
· Building a Proactive Safety Culture · Creating a Safety Vision · Commitment and Leadership · Safety Involvement · Enhancing Communication · Hazard Identification and Control · Incident Investigations · Safety Education and Training · Setting Expectations and Accountability · The Tools in the Safety Toolbox and How to Use Them |